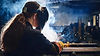
Erstellen
die Infrastruktur
von allem
Wir sind nach ISO 9001:2015 zertifiziert und CWB-zertifiziert. Wir fertigen Strukturkomponenten vom Entwurf bis zur Montage. Unser Sitz ist in Windsor, Ontario, im Herzen des nordamerikanischen Automobil- und Fertigungszentrums.
TECHNOLOGIE
Hohe Präzision,
Nahtlose Integration
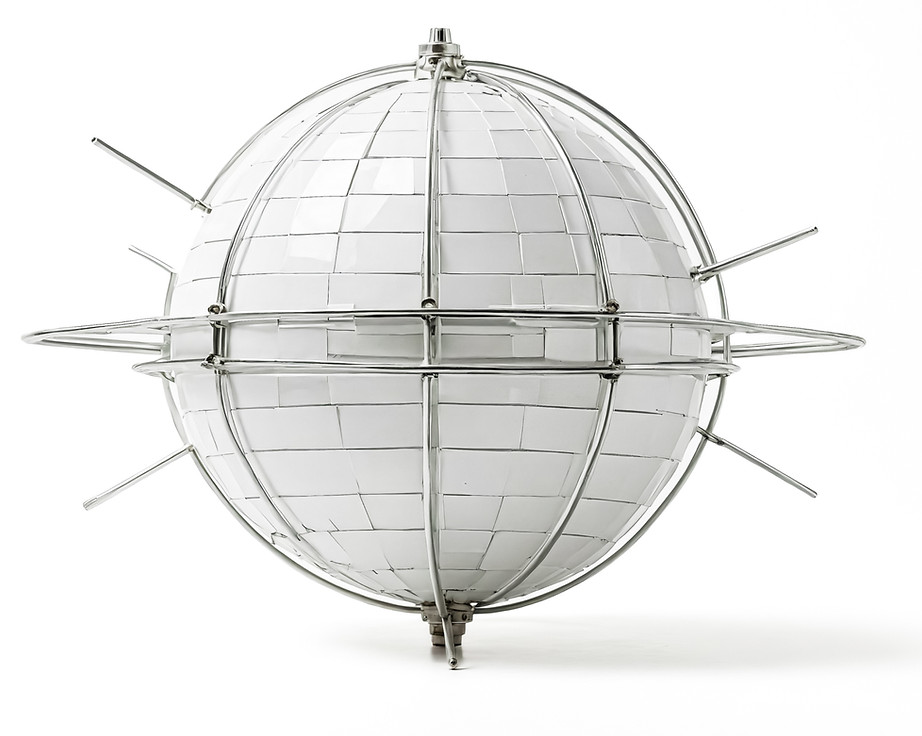
KERNKOMPETENZEN
• Sonderanfertigungen.
• Kohlenstoffstahl, Edelstahl.
• Bearbeitung und individuelle Endbearbeitung.
• Schweißen: WIG, MIG, Lichtbogen und Fusion.
• Qualitätskontrolle.
• Baugruppe, Unterbaugruppe.
• Kundenspezifisches Design, Bau nach Spezifikation.
• Industriedesigner, Elektriker, Maler und Schweißer.
• MIG- und WIG-Schweißgeräte.
• Plasmaschneider, Bandsäge, Drehbank, Flächenschleifmaschine.
• Übergroße Lackierkabine.
BENUTZERDEFINIERTE BAUGRUPPEN
Mechanische Komponenten:
Fachmännisch gefertigt, um genau Ihren Anforderungen zu entsprechen.
Strukturbaugruppen:
Langlebige und zuverlässige Lösungen für komplexe Projekte.
Fortschrittliche Schweißlösungen:
Präzisionsschweißen für robuste, langlebige Ergebnisse.
CNC-Bearbeitung und Blechbearbeitung:
Vom Prototyping bis zur Großserienproduktion.
End-to-End-Fertigung:
Umfassende Dienstleistungen vom Design bis zur Fertigstellung. Unsere hochmodernen Anlagen und unser kompetentes Team sorgen dafür, dass jede Komponente nahtlos integriert und leistungsoptimiert ist.

INNOVATION – STÄRKE SCHMIEDEN
Exzellenz in Industriequalität
Präzision in der Luft- und Raumfahrt
UMS | fabrication verfügt über langjährige Erfahrung in der Zusammenarbeit mit unseren Kunden, um das effektivste und funktionalste Endprodukt zu entwickeln. Dazu gehören unter anderem revolutionäre Teiletransportkonzepte, hocheffiziente Trägerlösungen und patentierbare modulare Rohbau-Montagelinien.
Wir sind stolz darauf, einen sorgenfreien Service anbieten zu können, bei dem der Kunde kritische Aspekte eines Projekts abgeben und sich darauf verlassen kann, dass wir ein meisterhaft gestaltetes Produkt liefern, bei dem die Qualität an erster Stelle steht.

ANWENDUNGEN
Fallstudien:
Herstellung

Flanschbiegestation
Brauchen
Ein Automobilzulieferer benötigte eine Bördelmaschine für Karosserieteile. Aufgrund der Komplexität des Bördelvorgangs und des hohen Produktionsvolumens sollte die benötigte Kantenbördelmaschine vollautomatisch sein. Die Maschine benötigte außerdem zusätzliche Funktionen wie automatische Werkzeugwechsler und programmierbare Steuerungen zur Steigerung von Effizienz und Genauigkeit.
1
Unter Einhaltung eines äußerst engen Zeitrahmens entwickelte UMS ein hochwertiges Gerät und übertraf letztendlich die ursprünglichen Erwartungen.
Lösung
3
Die benötigten Teile müssen maschinell präzise gefertigt werden. Die Maschine sollte Ecken und Kanten vermeiden, während Sicken das Blech verstärken und Referenzpunkte für die Ausrichtung bei Montage und Schweißen bieten. Die Maschine musste außerdem verschiedene Prüfungen durchführen, um sicherzustellen, dass der gesamte Prozess korrekt durchgeführt wurde.
Herausforderung
2
Als das Unternehmen unsere automatisierte Station einführte, erreichte es:
• Eine Steigerung der Produktionseffizienz um 25 %.
• Eine Reduzierung der Qualitätsfehler um 30 % (allein durch fehlerhafte Montage entstehen jährlich Kosten von über 120.000 $!).
Vorteile/ROI
4

Industriell
Crossover-Plattform
Brauchen
Die Hauptanforderung unseres Kunden war die Möglichkeit, innerhalb seiner Anlage von einer Seite zur anderen zu wechseln. Einige Prozesse finden in der Halle statt, andere direkt an der bereits laufenden Produktionslinie. Für dieses Projekt wünschte er sich drei Übergänge, um verschiedene Teile der Hauptproduktionslinie bedienen zu können.
1
Nach sorgfältiger Überprüfung der Abstände
An der Produktionslinie für die Automobilindustrie haben wir unter Berücksichtigung der Kundenanforderungen den optimalen Abstand für den Crossover ermittelt. Durch sorgfältiges Platzieren der Beine und Streben an der richtigen Stelle gelang es uns, Plattformen zu schaffen, die alle korrekt unterstützten, ohne den darunterliegenden Prozess zu beeinträchtigen.
Lösung
3
Eine der größten Herausforderungen waren die Abstände unter dem Crossover. Da es in der Automobilproduktionslinie einige Teile gab, die eine gewisse Höhe erreichen konnten, musste der Crossover über genügend Abstand verfügen, um für die Produktionslinie handhabbar zu sein, und gleichzeitig niedrig genug sein, um die anderen Strukturen darüber nicht zu beeinträchtigen.
Herausforderung
2
Als das Unternehmen das System einführte, erreichte es Folgendes:
• Eine Steigerung der Produktionseffizienz um 25 %.