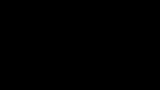
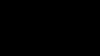
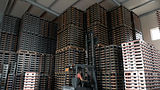
Dunnage Handling
Systems
Besoin
L'objectif de conception des systèmes de manutention de calage (Space Manager) est de fournir un tampon ou un point d'accès pour charger/décharger le flux de pièces entre les processus de la machine.
1
Developed high-quality equipment within tight deadline.
-
Cost Savings
-
Reduced Waste
-
Time Efficiency
-
Streamlined Operations
Solution
3
Les usines de fabrication étaient confrontées à des défis importants, principalement liés au processus fastidieux de séparation des cales vides et pleines. La méthode traditionnelle générait plusieurs inefficacités opérationnelles : de longues files d'attente imprévues de camions se formaient dans la zone de chargement en raison du mélange des conteneurs.
Défi
2
Faibles temps de cycle. Assemblage à grande vitesse.
Élimination des erreurs humaines.
Garantit une expédition de moulage acceptable au client.
Avantages/retour sur investissement
4
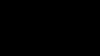

Flange Bender Station
Besoin
Un équipementier automobile avait besoin d'une machine à border les panneaux de carrosserie. Compte tenu de la complexité de l'opération et du volume de production élevé, les machines devaient être entièrement automatiques. Des fonctionnalités supplémentaires, telles que des changeurs d'outils automatiques et des commandes programmables, étaient également nécessaires pour accroître l'efficacité et la précision.
1
UMS a développé un équipement de haute qualité tout en respectant un délai extrêmement serré et en dépassant finalement les attentes initiales.
Solution
3
Les pièces requises par la machine, aux dimensions et à la forme précises, éliminaient les aspérités, tandis que le sertissage renforçait la tôle et fournissait des points de référence pour l'alignement lors de l'assemblage et du soudage. La machine devait également effectuer divers contrôles afin de garantir le bon déroulement de l'ensemble du processus.
Défi
2
Lorsque l'entreprise a adopté notre station automatisée, elle a obtenu :
• Une augmentation de 25 % de l’efficacité de la production.
• Une réduction de 30 % des erreurs de qualité (un mauvais assemblage coûte à lui seul plus de 120 000 $ par an !).
Avantages/retour sur investissement
4
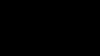
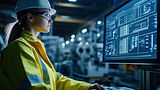
Avseal Installation
Probe/Inspection Station
Besoin
Un constructeur automobile a besoin de bouchons d'étanchéité Avseal installés sur des pièces avec une grande précision. En raison du volume important de ces bouchons, des centaines de millions de bouchons doivent être installés dans les applications industrielles.
1
Ce bouchon d'étanchéité en deux parties, rapide à installer, améliore la qualité et la sécurité dans les applications exigeantes, tout en simplifiant la préparation et l'installation des trous, réduisant ainsi les coûts d'assemblage. Les applications typiques incluent les blocs moteurs, les transmissions, les cylindres, les freins, les boîtes de vitesses, les systèmes pneumatiques, les blocs hydrauliques, les compresseurs et les pompes.
Solution
3
Ultimate Manufacturing a relevé le défi et développé un équipement de haute qualité, tout en respectant un délai extrêmement serré et en dépassant les attentes initiales. L'inspection microscopique des blocs moteurs rend la mesure et la caractérisation précises des propriétés de plus en plus complexes.
Défi
2
Lorsque l'entreprise a adopté notre système automatisé
station, ils ont réalisé :
• Une augmentation de 35 % de l’efficacité de la production.
• Une réduction de 40 % des erreurs de qualité (un mauvais assemblage coûte à lui seul plus de 150 000 $ par an !).
Avantages/retour sur investissement
4
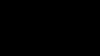

Industriel
Plateforme croisée
Besoin
La principale exigence de notre client était de pouvoir accéder à ses installations. Certains processus sont réalisés en atelier, et certains d'entre eux étaient réalisés directement sur sa ligne de production, déjà opérationnelle. Pour ce projet, il a demandé trois passerelles permettant de relier les différentes parties de la ligne de production principale.
1
Après avoir soigneusement vérifié les jeux
Sur la ligne de production automobile, nous avons trouvé le dégagement optimal pour le crossover, en dessous et au-dessus, en tenant compte des besoins de notre client. En plaçant soigneusement les pieds et les renforts à leur position idéale, nous avons créé des plateformes qui les soutenaient correctement sans interférer avec le processus.
Solution
3
One of the biggest challenges was the clearances under the crossover, since the automotive production line had some parts that can reach certain height, the crossover had to have enough clearance to be manageable for the production line, and short enough not to interfere with the other structures above it.
Défi
2
Lorsque l'entreprise a adopté le système, elle a obtenu :
• Une augmentation de 25 % de l’efficacité de la production.