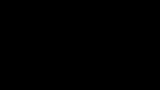
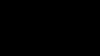
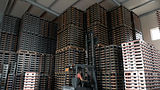
Movimentazione del pagliolo
Sistemi
Bisogno
L'intento progettuale dei sistemi di movimentazione dei carichi (Space Manager) è quello di fornire un buffer o un punto di accesso per caricare/scaricare il flusso di pezzi tra i processi delle macchine.
1
Ha sviluppato attrezzature di alta qualità rispettando tempi di consegna ristretti.
Risparmio sui costi
Rifiuti ridotti
Efficienza temporale
Operazioni semplificate
Soluzione
3
L'impianto di produzione ha dovuto affrontare sfide significative principalmente a causa del lungo processo di separazione del dunnage vuoto o pieno accatastato. Il metodo tradizionale ha creato diverse inefficienze operative: lunghe code di camion non pianificate si sono formate nell'area di carico a causa della miscelazione dei container.
Sfida
2
Tempi di ciclo bassi. Assemblaggio ad alta velocità.
Eliminato l'errore umano.
Garantisce una spedizione accettabile del pezzo fuso al cliente.
Vantaggi/ROI
4
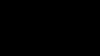

Stazione piegatrice per flange
Bisogno
Un fornitore del settore automobilistico richiedeva una macchina per flangiatura per pannelli di carrozzeria. Le macchine per flangiatura dei bordi richieste dovevano essere completamente automatiche a causa della complessità dell'operazione di flangiatura e dell'elevato volume di produzione. La macchina richiedeva anche caratteristiche aggiuntive come cambi utensile automatici e controlli programmabili per aumentare efficienza e precisione.
1
La UMS ha sviluppato un'apparecchiatura di alta qualità rispettando una scadenza estremamente ravvicinata e superando in definitiva le aspettative iniziali.
Soluzione
3
Le parti richieste dalla macchina con dimensioni precise e la macchina dovrebbe eliminare i bordi ruvidi, mentre la bordatura rinforza la lamiera e fornisce punti di riferimento per l'allineamento durante l'assemblaggio e la saldatura. La macchina era anche tenuta a eseguire vari controlli per garantire che l'intero processo fosse eseguito correttamente.
Sfida
2
Quando l'azienda ha adottato la nostra stazione automatizzata, ha ottenuto:
• Un aumento del 25% dell'efficienza produttiva.
• Una riduzione del 30% degli errori di qualità (solo un assemblaggio errato costa più di 120.000 dollari all'anno!).
Vantaggi/ROI
4
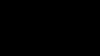
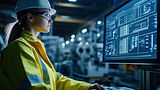
Installazione Avseal
Stazione di sonda/ispezione
Bisogno
Per un produttore automobilistico sono necessari i tappi di tenuta ciechi Avseal installati su parti con elevata precisione. A causa del grande volume, centinaia di milioni di tappi devono essere installati in applicazioni industriali.
1
Questo tappo di tenuta in due pezzi a rapida installazione migliora la qualità e la sicurezza in applicazioni impegnative, semplificando al contempo la preparazione e l'installazione dei fori, riducendo i costi di assemblaggio. Le applicazioni tipiche includono blocchi motore, trasmissioni, cilindri, freni, cambio, sistemi pneumatici, blocchi idraulici, compressori e pompe.
Soluzione
3
Ultimate Manufacturing ha raccolto la sfida e ha sviluppato un pezzo di equipaggiamento di alta qualità, rispettando una scadenza estremamente ravvicinata e superando in definitiva le aspettative iniziali. A causa dell'ispezione su scala microscopica richiesta sui blocchi motore, la capacità di misurare e caratterizzare accuratamente le proprietà diventa sempre più impegnativa.
Sfida
2
Quando l'azienda ha adottato il nostro sistema automatizzato
stazione, hanno ottenuto:
• Un aumento del 35% dell'efficienza produttiva.
• Una riduzione del 40% degli errori di qualità (solo un assemblaggio errato costa più di 150.000 dollari all'anno!).
Vantaggi/ROI
4
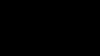

Industriale
Piattaforma crossover
Bisogno
Il requisito principale del nostro cliente era la capacità di attraversare da un lato all'altro all'interno della loro struttura. Ci sono alcuni processi eseguiti sul pavimento e alcuni di questi processi sono stati eseguiti direttamente sulla loro linea di produzione, che era già in funzione. Hanno richiesto per questo progetto tre attraversamenti per poter attraversare in diverse parti della linea di produzione principale.
1
Dopo aver controllato attentamente le distanze
della linea di produzione automobilistica, abbiamo trovato la migliore distanza per il crossover sotto e sopra, tenendo conto delle esigenze del nostro cliente. Posizionando con cura le gambe e i rinforzi nella posizione corretta, siamo riusciti a creare piattaforme in modo che tutte fossero supportate correttamente senza interferire con il processo sottostante.
Soluzione
3
Una delle sfide più grandi era rappresentata dagli spazi liberi sotto il crossover: poiché la linea di produzione automobilistica aveva alcune parti che potevano raggiungere una certa altezza, il crossover doveva avere abbastanza spazio libero per essere gestibile dalla linea di produzione e abbastanza basso da non interferire con le altre strutture soprastanti.
Sfida
2
Quando l'azienda ha adottato il sistema, ha ottenuto:
• Un aumento del 25% dell'efficienza produttiva.