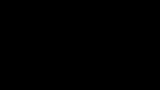
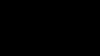
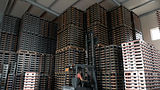
Dunnage Handling
Systems
必要
ダネッジ処理システム (スペース マネージャー) の設計目的は、機械プロセス間の部品フローをロード/アンロードするためのバッファーまたはアクセス ポイントを提供することです。
1
Developed high-quality equipment within tight deadline.
-
Cost Savings
-
Reduced Waste
-
Time Efficiency
-
Streamlined Operations
解決
3
製造工場は、主に空のダンネージと満載のダンネージを分離する時間のかかるプロセスが原因で、大きな課題に直面していました。従来の方法では、コンテナが混在しているために、積載エリアに予定外の長いトラックの列ができるなど、いくつかの運用上の非効率が生じていました。
チャレンジ
2
サイクルタイムが短く、組み立てが高速です。
人為的ミスを排除しました。
顧客への許容可能な鋳造品の出荷を保証します。
メリット/ROI
4
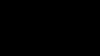

Flange Bender Station
必要
ある自動車部品メーカーは、車体パネル用のフランジ加工機を必要としていました。フランジ加工作業の複雑さと生産量の高さから、エッジフランジ加工機は完全自動化が求められていました。また、効率と精度を高めるために、自動工具交換装置やプログラム可能な制御などの追加機能も必要でした。
1
UMS は、非常に厳しい納期を守りながら、最終的には当初の期待を上回る高品質の機器を開発しました。
解決
3
機械に要求される部品は正確な寸法を持ち、粗いエッジを排除する一方で、ビーディングは板金を強化し、組み立てと溶接中の位置合わせのための参照点を提供します。また、機械は、プロセス全体が正しく完了したことを確認するために、さまざまなチェックを実行する必要がありました。
チャレンジ
2
当社が自動化ステーションを導入した結果、次のような成果が得られました。
• 生産効率が 25% 向上しました。
• 品質エラーが 30% 削減されました (組み立てミスだけでも年間 12 万ドル以上のコストがかかります)。
メリット/ROI
4
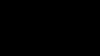
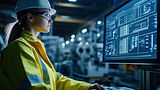
Avseal Installation
Probe/Inspection Station
必要
自動車メーカーでは、高精度で部品に取り付けられる Avseal ブラインド シーリング プラグを必要としています。産業用途では、量が多いため、何億個ものプラグを取り付ける必要があります。
1
この迅速に設置できる 2 ピースのシーリング プラグは、要求の厳しい用途での品質と安全性を向上させると同時に、穴の準備と設置を簡素化し、組み立てコストを削減します。代表的な用途には、エンジン ブロック、トランスミッション、シリンダー、ブレーキ、ギア ボックス、空気圧システム、油圧ブロック、コンプレッサー、ポンプなどがあります。
解決
3
Ultimate Manufacturing 社は、この課題に立ち向かい、非常に厳しい納期を守りながら、最終的には当初の期待を上回る高品質の装置を開発しました。エンジン ブロックには顕微鏡レベルの検査が必要なため、特性を正確に測定して特徴付けることがますます困難になっています。
チャレンジ
2
当社が自動化を導入したとき
駅で彼らは次のことを達成しました:
• 生産効率が 35% 向上しました。
• 品質エラーが 40% 削減されました (組み立てミスだけでも年間 15 万ドル以上のコストがかかります)。
メリット/ROI
4
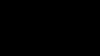

産業
クロスオーバープラットフォーム
必要
お客様からの主な要望は、施設内で一方から他方へ横断できることでした。フロアで行われるプロセスもいくつかあり、これらのプロセスの一部は、すでに稼働している生産ラインで直接行われていました。このプロ ジェクトでは、メイン生産ラインのさまざまな部分で横断できるように 3 つのクロスオーバーを要求されました。
1
クリアランスを慎重に確認した後
自動車生産ラインのクロスオーバーの下と上には、お客様のニーズを考慮した最適なクリアランスが確保されています。脚と支柱を適切な位置に慎重に配置することで、その下の工程を妨げることなく、すべてが正しくサポートされるプラットフォームを作成することができました。
解決
3
One of the biggest challenges was the clearances under the crossover, since the automotive production line had some parts that can reach certain height, the crossover had to have enough clearance to be manageable for the production line, and short enough not to interfere with the other structures above it.
チャレンジ
2
同社がこのシステムを導入した結果、以下の成果が得られました。
• 生産効率が 25% 向上しました。